Etats financier
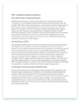
Cette méthode se base principalement sur le rapport eau/ciment prescrit dans les spécifications, afin e trouver les autres composantes qu’il faudra ajouter. Les spécifications pour le béton que l’on doit produire sont une résistance à la compression de 35 empan à 28 jours avec un affaissement de 80 ± 30 mm. En sachant que le béton sera utilisé pour fabriquer des trottoirs, on peut en déduire de premier boy vérifie 1 empara 23, 2011 21 pages par son exposition aux conditions extérieures du cubée, qu’il devra résister au cycle de gel-dégel, ainsi qua des écarts de températures élevés.
De plus, on sait qu’un trottoir représente la catégorie C-2. À partir de ces rapport eau/ciment devra être d’environ 0,39. Par contre, euro ce laboratoire, un rapport de 0,4 sera accepté. Il faut ensuite savoir la grosseur nominale des granules et les proportions entre les gros granules et le sable. Ces valeurs ont été données, soit une grosseur nominale maximale des gros granules de 14 mm et un rapport de 60 % de pierres pour 40 % de sable. AI est à noter que deux grosseurs de pierres ont été utilisées à ratio égal, soit de la pierre de 2,5-10 mm de diamètre et de 5-14 mm.
Alors, en sachant que le rapport eau/ciment exigé est de 0,4, la masse d’eau qui devra être mise dans le mélange est simplement de 4 kg et celle du ciment de 10 kg. Afin ‘obtenir une variabilité intéressante avec ce petit rapport eau/ciment, 25 ml d’adjuvant réducteur d’eau devra être ajouté, ainsi que 8 ml d’adjuvant entraîneur d’air afin de respecter la teneur en air désirée. Dans le cas des granules, nous avons utilisé la méthode d’essais et erreurs.
Ce qui veut dire que pour chaque pelleté de sable nous ajoutions 3 pelletés de chaque granules, afin de respecter notre ratio de sable et granules, et ce jusqu’ obtention d’une consistance qui semblait répondre à nos exigences. C’est-à-dire un affaissement d’environ 80 mm. Une fois notre béton bien mélangé, nous avons procédé aux essais pour déterminer les caractéristiques de notre mélange. Tout d’abord, le test d’affaissement a été effectué. Pour que cet es caractéristiques de notre mélange. Tout d’abord, le test d’affaissement a été effectué. Pour que cet essai soit valide, il faut qu’il respecte quelques règles.
Premièrement, il doit être effectué à l’aide d’un moule de forme conique ouvert aux deux extrémités avec des diamètres de 200 mm et 1 00 mm respectivement pour la base et le dessus. La hauteur de ce moule doit être 300 mm. Un pourvoir en acier de 16 mm de diamètre dont la hauteur se situe 450 et 600 mm est aussi nécessaire. De plus, l’hémisphère du pourvoir doit avoir un diamètre de mm. Finalement, les seuls autres instruments que nous avons besoin est une truelle et une barre d’rasséréna. La première étape consiste à humecter la paroi intérieure du moule pour éviter que le béton y adhère.
Ensuite on doit poser les deux pieds sur les appuis prévus à cet effet, pour empêcher que le béton fuie en dessous du moule. Une fois ces deux étapes effectuées le remplissage du béton peut commencer. Le remplissage se fait en trois parties de même volume. Entre chaque partie, il faut pilonner le béton 25 fois avec le pourvoir en effectuant la moitié de ces coups sur les parois et le reste en spirale vers le centre. Ces coups doivent pénétrer la couche de béton inférieure d’environ 25 mm. Lors de la troisième couche, il est préférable d’ajouter un surplus de béton pour créer un léger excès au-dessus du cône.
Il faut cependant araser cet excès et nettoyer les parois du moulu cône. AI faut cependant araser cet excès et nettoyer les parois du moule. Il faut ensuite retirer le moule d’une façon continue et verticale en plus ou moins 5 secondes. Pour mesurer l’affaissement, il suffit de renverser le moule côté du mélange et de mesurer la différence de hauteur entre le moule et le mélange. Cependant, pour que la norme AI. 2-CC, où ont été puisés les renseignements précédents, soit respecté, il faut que l’essai soit réalisé en moins de 10 minutes.
Dans notre cas, la mesure de l’affaissement a été d’environ 130 mm, ce qui est nettement au-dessus de l’affaissement exigé de 80 ± 30 mm. Il aurait donc fallu ajouter encore des granules, afin de solidifier le béton frais. De plus, la contrainte de temps de AI minutes n’ pas été respectée, ce qui a peut-être eu des effets négatifs sur le résultat. Dans ce cas, l’affaissement n’ pu être que plus petit que la valeur réelle, puisque e béton a eu un peu plus de temps pour prendre que ce que la norme exigeait.
Aussi, selon la norme, il aurait fallu réaliser deux essais afin de pouvoir comparer les deux résultats. Un autre essai consiste simplement à mesurer la température du béton, selon la norme SAIT C 1064. Cette norme précise que la partie du thermomètre qui mesure la température doit être submergé d’au minimum 75 mm de chaque côté et que e béton doit être légèrement pressé afin que la température de l’air ambiant n’influence pas la empêtrera me légèrement pressé afin que la température de l’air ambiant n’influence pas la température mesurée.
Il faut ensuite laisser dans cette position le thermomètre pendant un minimum de 2 minutes et la mesure doit être prise en déc. de 5 minutes après l’obtention de la gâchée. La température doit être précise au 0. 5 oc près. Dans le cas de notre gâchée, une mesure de 20,6 oc a été mesurée, ce qui est légèrement sous la température de la pièce. Cette température signifie donc que la réaction chimique n’était pas encore très avancée, car cette réaction est ésotérique. Ainsi, le béton a tendance à se réchauffer au fur et à mesure que le temps passe jusque’ ce que la réaction soit terminée.
Le troisième essai est celui de la mesure et du calcul de la masse volcanique, selon la norme AI. 2-CC. Pour trouver la masse volcanique, il faut mesurer à l’aide d’une balance (précision de kg) un volume précis de béton. Le calcul s’effectue en divisant la masse par le volume. Le volume précis est déterminé à l’aide du contenant qui servira aussi pour trouver la teneur en air. Ce contenant peut contenir 7,0534 L de béton, ce qui équivaut à environ 0,0070534 mm. D’abord, il est nécessaire de peser le contenant vide et la masse mesurée a été de 3,45 kg.
On peut par la suite le remplir de béton toujours en trois couches de même volume et en pilonnant entre chaque couche. De plus, lors de cette manipulation, il est préférable de donner une dizaine de entre chaque couche. De plus, lors de cette manipulation, il est préférable de donner une dizaine de coups sur les côtés du contenant, à l’aide d’une petite masse par exemple, après chaque pilonnage pour que les trous causés par ce dernier se referment. À la dernière couche, il est encore sébile d’ajouter du béton pour qu’il ait un petit surplus au dessus du contenant.
Ce surplus peut par la suite être araser. Juste avant de prendre la pesé avec le béton, il faut s’assurer de bien nettoyer les rebords du contenant pour ne pas fausser les données de volume. Pour notre part, la masse totale a été de 19,45 kg. Donc, la masse de béton contenu dans 7,0534 L était de 19,45 kg – 3,45 kg = 16,00 kg. La masse volcanique du béton de cette gâchée était donc de kg/mm. Le dernier essai qui doit être effectué sur le béton frais est celui de la teneur en air. La méthode de pression d’air est elle qui est utilisée, selon la norme AI. -CC. L’appareillage nécessaire est un contenant à volume (le même qu’utilisé lors du précédent essai), un couvercle hermétique avec un dispositif permettant d’exercer une pression sur le béton et d’observer les effets sur le volume de celui-ci, à l’aide d’un cadran du manomètre précis à 0,2% entre des teneurs en air de O à AI faut d’abord remplir le contenant, ce qui a déjà été fait à l’essai précédent, et le fermer hermétiquement. En ouvrant les robinets, il est possible de chasser l’air qui se et le fermer hermétiquement.
En ouvrant les robinets, il est sébile de chasser l’air qui se trouve au-dessus du béton en injectant de l’eau dans le petit robinet jusqu’ ce que celle-ci ressorte par l’autre robinet. AI faut ensuite fermer les robinets et pomper de l’air dans la chambre pour atteindre la pression voulue, dans le cas de l’appareil utilisé, il faut aller à . 2 % sous le point O. Cette valeur, trouvée expérimentalement à l’aide de l’eau, est due au fait qu’il reste toujours une petite partie d’air au niveau du scellant entre la chambre d’air et le récipient.
Une fois la pression obtenue, il faut ensuite ouvrir rapidement la soupape permettant de retirer tout l’air contenu dans le copient. Le cadran indique alors une valeur, précisément celle de la teneur en air. La teneur en air que nous avons obtenue en laboratoire est de 6,5 %, ce qui respecte les spécifications, qui exigeaient une teneur entre 5 et 8 % d’air. Finalement, il est possible de déterminer les proportions effectives du mélange final. Pour cela, il faut d’abord calculer la masse de chacun des constituants qui ont été utilisés.
Dans le cas de l’eau, elle a toute été utilisée, ce qui veut dire que 4 kg d’eau se retrouve dans la gâchée. C’est le même principe pour le ciment, où AI kg ont été utilisés. Pour ce qui est du sable, initialement il y en avait 26,10 kg et il en est resté 13,6 kg. Il a donc par soustraction 12,5 kg dans la gâchée. C’est le m 26,10 kg et il en est resté 13,6 kg. AI ha donc par soustraction 12,5 kg dans la gâchée. C’est le même calcul pour es deux gros granules, donc la gâchée contient pour la pierre 2,5-10 et la pierre 5-14 respectivement 9,70 et 9,5 kg.
Sachant la masse de chacun des constituants, il est possible de déterminer la masse totale de la gâchée en les additionnant tous ensemble, ce qui donne une masse de 45,70 kg. À partir de cette donnée, il est possible de trouver lue est le volume de béton créé. Pour se faire, il faut diviser la masse de la gâchée par la masse volcanique trouvée précédemment. On obtient alors un volume de 0,020146 mg. De plus, en divisant la masse utilisée de chacun des constituants par ce volume, on peut déterminer la masse par mètre cube de béton de ces constituants.
Bref, les proportions effectives sont de 198,54 kg/mm ou 0,19854 L/mm d’eau, 496,37 kg/mm de ciment, 620,46 kg/mm de sable, 481 kg/mm de gros granules (2,5-10) et 471 kg/mm de gros granules (5-14). Il est aussi possible de déterminer, si le ratio sable/gros granules a été respecté n divisant la masse de sable par la masse totale de granules (sable + gros granules). On obtient une proportion de 39,4 % de sable, ce qui est presque exactement le ratio voulu qui était de 400/0.
Afin de réaliser des essais sur le béton durci, il faudra bien sûr fabriquer des éprouvettes d’essais. Pour se faire, deux différents types de moules seront utilisés, I fabriquer des éprouvettes d’essais. Pour se faire, deux différents types de moules seront utilisés, l’un cylindrique et l’autre rectangulaire. Les moules cylindriques utilisés pour les essais en compression et en traction par vendange voient, selon la norme AI. 2-CC, avoir une hauteur deux fois plus grande que le diamètre. Pour ce laboratoire, un diamètre de 100 mm et une hauteur de 200 mm sont utilisés.
Avant de remplir le moule de béton, il est recommandé d’appliquer une mince couche d’huile. Pour les remplir, il faut suivre la méthode énoncée précédemment soit celle des trois couches de même volume consolidées à l’aide d’un pourvoir. Il est à noter que le moulage doit selon la norme, s’effectuer en moins de 20 minutes après l’échantillonnage. Finalement, après avoir araser le surplus au dessus du moule, il faut mettre en cure es éprouvettes à une température de 23 ± 2 oc en les recouvrant de manière à empêcher toute évaporation.