AMDEC Moyen
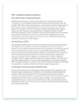
AMDEC-Moyen par Michel RIDOUX Consultant A p RAVE Division Qualité – Organisation – Maintenance Disponibilité 2. Sni* to View Analyse des modes d et de leur criticité . Trais types d’AMDEC….. 2. 1. 1 AMDEC Produit… 2. 1. 2 AMDEC- process 2. 1. 3 AMDEC- Moyen de production . Terminologie Caractéristiques essentielles de l’AMDEC . Buts de l’AMDEC.. fets finaux… 2. 5. 7 Suivi 3 actions visant à éradiquer les dysfonctionnements.
L’AM DEC (Analyse des Modes de Défaillance, de leur Effets et de leur Criticité) est un outil méthodologique permettant l’analyse systématique es dysfonctionnements potentiels d’un produit, d’un procédé ou d’une installation. Cette démarche offre un cadre de travail rigoureux en groupe associant les compétences et expériences de l’ensemble des acteurs concernés par l’amélioration de performance de l’entreprise. L’AMDEC permet de mobiliser les ressources de l’entreprise autour d’une préoccupation commune à tous : l’amélioration de la disponibilité de routil de production.
Toute reproduction sans autorisation du Centre français d’exploitation du droit de copie est strictement interdite. @ Techniques de l’Ingénieur, traité L’entreprise industrielle AG 4 220-1 AMDEC – MOYEN La méthode AM DEC a été utilisée originellement dans le traitement des risques potentiels inhérents aux activités de production de l’armement nucléaire. Progressivement, elle a été adaptée à l’ensemble des activités à risques (nucléaire civil ; domaine aéronautique, spatial ; grands travaux), puis a été intégrée dans les projets industriels.
De nos jours, son emploi est très répandu PAGF 3 l’AMDEC offre une garantie supplémentaire pour l’entreprise industrielle de l’amélioration de ses performances. Son utilisation très tôt en phase de conception (du produit, du rocédé ou de l’outil de production) révèle la volonté de l’entreprise d’anticiper les problèmes potentiels plutôt que d’en subir les conséquences à terme. 1. Disponibilité La disponibilité des moyens de production est leur aptitude à être en état d’accomplir une mission déterminée dans des conditions données, à un instant donné ou pendant un intervalle de temps donné.
Elle s’exprime par le ratio : temps de fonctionnement –E temps de fonctionnement + temps d’arrêt La diminution des stocks intermachines dans les flux de production, ajoutée à l’automatisation et à l’informatisation des oyens de production, pose avec plus d’acuité le problème de la maîtrise de disponibilité avec, pour objectifs, la rentabilisation des investissements industriels. L’analyse de disponibilité permet d’identifier globalement les sources de perte de performance en production et de déterminer actions à mener (amélioration de la fiabilité et/ou amélioration de la maintenabilité).
Le concepteur et l’exploita 3 s de production disposent situation initiale. 2. Analyse des modes de défaillance, de leurs effets et de leur criticité L’Analyse des modes de défaillance, de leurs effets et de leur riticité (AMDEC) est une méthode d’analyse prévisionnelle de la fiabilité qui permet de recenser systématiquement les défaillances AG 4 220-2 potentielles d’un dispositif puis d’estimer les risques liés ? l’apparition de ces défaillances, afin d’engager les actions correctives ? apporter au dispositif.
L’AMDEC a fait son apparition en France dans le domaine aéronautique (Concorde puis Airbus ) au cours des années 1960 (cf. encadré). Introduite dans Findustrie manufacturière de série depuis les années 1980, son application y reste, encore aujourd’hui, très répandue. L’industrie de process pour sa part et en œuvre plus facilement la méthode HAZOP dont les fondements s’inspirent de l’AMDEC. Domaines d’application de l’AMDEC Années 1950 : la méthode FMECA (Fallure Modes, Effects and Criticality Analysis) est introduite aux États-Unis dans le domaine des armes nucléaires.
Années 1960 : PAGF s 3 types d’AMDEC Il existe globalement trois types d’AMDEC suivant que le système analysé est . le produit fabriqué par l’entreprise ; — le processus de fabrication du produit de l’entreprise ; le moyen de production intervenant dans la production du produit de l’entreprise. AMDEC – MOYEN 2. 1. AMDEC-Produit L’AMDEC-Produit est utilisée pour raide à la validation des études de définition d’un nouveau produit fabriqué par l’entreprise. Elle est mise en œuvre pour évaluer les défauts potentiels du nouveau produit et leurs causes.
Cette évaluation de tous les défauts possibles permettra d’y remédier, après hiérarchisation, par la mse en place d’actions correctives sur la conception et préventives sur l’industrialisation. 2. 1. 2 AM DEC-Process L’AMDEC-Process est utilisée pour étudier les défauts potentiels d’un produit nouveau ou non, engendrés par le processus de abrication. Elle est mise en œuvre pour évaluer et hiérarchiser les défauts potentiels d’un produit dont les causes proviennent de son processus de fabrication.
S’il s’agit d’un nouveau procédé YAMDEC-Process en permettra l’optimisation, en visant la es causes de défaut PAGF 6 3 sa conception ou pendant sa phase d’exploitation. • À la conception du moyen de production, la réalisation dune AMDEC permet de faire le recensement et l’analyse des risques potentiels de défaillance qui auraient pour conséquence d’altérer performance globale du dispositif de production, l’altération de erformance pouvant se mesurer par une disponibilité faible du mayen de production. Dans ce cas de figure, l’analyse est conduite sur la base des plans et/ou prototypes du moyen de production.
L’objectif est généralement ici de : modifier la conception — lister les pièces de rechange ; prévoir la maintenance préventive. Pour un moyen de production en cours d’exploitation, la réalisation d’une AMDEC permet l’analyse des causes réelles de défaillance ayant pour conséquence l’altération de la performance du dispositif de production. Cette altération de performance se mesure par une disponibilité faible du moyen de production. Dans ce cas de figure, l’analyse est conduite sur le site, avec des récapitulatifs des pannes, les plans, les schémas, etc. onnaître l’existant : — améliorer ; optimiser la maintenance (gamme, procédures, etc. ) ; — optimiser la conduite (procédures, modes dégradés, etc. ). Dans la suite de cet article, seule l’AMDEC-Mayen est étudiée. Globalement il n’existe pas de différence fondamentale de fond avec les autres champs d’application (produit et process). • Fonction La norme NF EN 1325-1 définit la notion de fonction comme l’action d’un produit ou de ses constituants exprimée exclusivement n termes de finalité.
Une être : PAGF 7 3 d’un utilisateur donné ; — une fonction technique : action interne au produit (entre ses constituants) définie par le concepteur-réalisateur, dans le cadre d’une solutlon pour assurer les fonctions de service ; — une fonction principale : fonction pour laquelle le produit ou le constituant est créé ; — une fonction secondaire (ou complémentaire) : toute fonction autre que la ou les fonctions principales ; — une fonction d’estime (ou esthétique) : ces fonctions, du type « être esthétique » ou « être en or » ou le paraître, n’ont pas d’usage ? proprement parler ; une fonction de contrainte : elle traduit des réactions ou des résistances à des éléments du milieu extérieur, la contrainte étant l’action de ce milieu extérieur sur le moyen de production étudié. Exemple : trier, écrire, guider, transporter. • Critère d’appréciation C’est le critère retenu pour apprécier la manière dont une fonction est remplie ou une contrainte respectée. Les fonctions seront nommées à chaque fois que cela est possible en utilisant un verbe plus un nom qui ont des paramètres mesurables.
Exemple : écrire sur une surface plate verticale de couleur lanche, transporter cinq personnes à une vitesse moyenne de 90 km/h. Défaillance Une défaillance est la cessation de l’aptitude d’une entité ? accomplir une fonction requise (norme X 60-500). une défaillance désigne tout ce qui paraît anormal, tout ce qui s’écarte de la norme de bon fonctionnement. La défaillance peut être complète ; il s’agit de la cessation de la réalisation de la fonction du dispositif. La défaillance peut être partielle il s’a it de l’altération de la réalisation de la fonction d PAGF E 3 circuit d’éclairage (défaillance partielle de la voiture et complète u dispositif). ?? Mode de défaillance un mode de défaillance est la manière par laquelle un dispositif peut venir à être défaillant, c’est-à-dire à ne plus remplir sa fonction. Le mode de défaillance est toujours relatif à la fonction du dispositif. Il s’exprime toujours en termes physiques. Exemple : blocage, grippage, rupture, fuite, etc. • Cause de défaillance Une cause de défaillance est l’événement initial pouvant conduire à la défaillance d’un dispositif par l’intermédiaire de son mode de défaillance. Plusieurs causes peuvent être associées à un même mode de défaillance. ne même cause peut provoquer plusieurs modes de défaillance.
Exemple : encrassement, corrosion, dérive d’un capteur, etc • Effet de la défaillance 2. 2 Terminologie Un certain nombre de notions sont utilisées dans l’AMDEC. Il est important de les connaitre parfaitement afin de comprendre précisément le fonctionnement de l’AMDEC et d’en assurer la meilleure application possible. L’effet d’une défaillance est, par définition, une conséquence subie par l’utilisateur. Il est associé au couple (mode-cause de défaillance) et correspond à la perception finale de la défaillance ‘utilisateur. Exemple : arrêt de production, détérioration d’équipement, explosion, pollution, etc. d’exploitation du droit de ement interdite. igoureuse qui permet une recherche systématique • — des modes de défaillance d’un moyen de production (par exemple : perte d’une fonction, dégradation dans la réalisation d’une fonction, réalisation intempestive de la fonction) ; des causes de défaillance générant les modes de défaillance. Ces causes peuvent se situer au niveau des composants du moyen de production ou être dues à des sollicitations extérieures ; es conséquences des défaillances sur le moyen de production, sur son environnement, sur le produit ou sur l’homme ; des moyens de détection pour la prévention et/ou la correction des défaillances. La méthode est qualifiée d’inductive car son point de départ est la recherche des événements élémentaires pour en déduire les conséquences finales. Par opposition, les méthodes déductives consistent à analyser la conséquence finale pour en rechercher les élémentaires.
L’AM DEC est une méthode de travail de groupe qui réunit : — des compétences dans le domaine des études et des méthodes • ?? des expériences dans le domaine de la maintenance, des méthodes, de la fabrication et de la qualité. La création du groupe de travail permet l’apport « vivant » de la connaissance, de l’expérience et du bon sens. Elle permet également la réunion des personnes qui n’ont pas tendance à se rencontrer naturellement dans un esprit constructif. La constitution du groupe de travail facilite l’association des différents acteurs ? l’œuvre commune qu’est la construction de la disponibilité. Une cause de défaillance étant su osée apparue, le mode de détection est la manière utilisateur (opérateur et/