MRP FINAL FINAL PERFECT 1 1
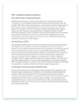
L’Aéronautique ANTONIOS Philippe LACHGUER Omar M. LOMBARDOT DUMAN Daniel 2 Table des matières Introduction l/ Gestion des stocks MRP FINAL FINAL PERFECT 1 1 Premium gy sadoIgg2 anpenA II, 2015 28 pages Gestion de Production MRP et Gestion des Stocks Sni* to View 4 or28 A) B) C) 1) Définition 6 Les principaux systèmes Introduction au MRP Historique de gestion 7 des stocks 8 (niveau opérationnel) 15 1) Types de nomenclature 2) Décomposition du PDP nomenclature ou explosion 3) E) L’ordonnancement 17 Pilotage des ateliers et suivi Ill/ Le MRP aujourd’hui 21 A) Avantages et inconvénients et la 16 19 différences
B) Nouvelle méthode avec le JAT complémentarité 25 BIBLIOGRAPHIE ET WEBOGRAPHIE 28 La gestion de production est plus facile de définir par ses objectifs que par ses composantes tant elles sont nombreuses : conception de processus de production, gestion des stocks, approvisionnement, mise en œuvre d’une politique de qualité, organisation et planification de la fabrication Ces composantes servent à satisfaire les objectifs de l’entreprise qui sont de fabriquer au moindre coût des produits de ualité adaptés aux désirs des consommateurs, et mis ? PAGF OF coût des produits de qualité, adaptés aux désirs des onsommateurs, et mis à leur disposition dans des délais raisonnables. Désormais la réponse optimale au consommateur est au cœur de la stratégie des entreprises et les responsables de la gestion de la production doivent remplir ces 4 objectifs. Depuis les Trente glorieuses l’entreprise est plongée dans un environnement concurrentiel, technologique et réglementaire.
La firme industrielle doit répondre à ces différents objectifs en prenant en considération un certain nombre de contraintes. par exemple, le passage aux 35 heures, la législation dans le domaine du transport aérien ou encore la demande et les xigences constante croissance des clients sont des facteurs ? prendre en compte. Il faut donc anticiper pour rester efficace et cela a conduit les entreprises ? adopter des nouveaux modèles de gestion des stocks. Il existe plusieurs modèles de l’organisation de la production (Planification des besoins en composants, SMED (single minute exchange of die), le principe des 5S, le Lean Management Kanban ) pour répondre aux différents besoins et contraintes des entreprises.
On ne peut pas gérer la fabrication d’Airbus, de satellites ou encore de bagages de la même façon, il est donc logique d’avoir des modèles de production différents. De la même façon, les clients n’ont pas les mêmes objectifs en termes de délais et d’exigence en termes de qualité Les producteurs doivent tenir compte de ses éléments dans leur organisation. Parmi ces modèles, la méthode MRP Material Requirements Planning) consiste à la PAGF question suivante : en quoi le MRP constitue-t-il une bonne méthode de gestion des stocks pour le secteur de l’aéronautique ? C’est la question à laquelle nous tenterons de répondre tout au long de notre étude. Pour cela, dans une première partie nous allons définir le MRP et étudier son évolution.
Nous nous ttarderons ensuite sur les principes du MRP notamment par le fonctionnement de celui-ci. Puis en dernier lieu, nous procéderons à l’énumération des avantages et des inconvénients de cette méthode. Le secteur Aéronautique Le secteur aéronautique et spatial concerne les industries des secteurs de l’aéronautique et de l’espace, mais également l’industrie de l’armement. Le secteur aéronautique regroupe les activités de conception, de fabrication et de commercialisation des aéronefs (avions, hélicoptères, drones, etc. ) et des équipements spécifiques associés. Technologiquement et industriellement, les industries éronautiques, spatiales et militaires sont très proches.
C’est ce point qui fait de l’industrie de l’aéronautique une industrie stratégique pour les Etats puisqu’elle est significative de leur puissance militaire et donc aussi de leur influence internatlonale. Ainsi, la part de la dans cette industrie de pointe est très importante. par exemple, en 2002, les entreprises européennes ont investie de leur chiffre d’affaire pour élaborer de nouvelles technologies. Dans ce secteur, la deman es Etats (en particulier que l’industrie de l’aéronautique a connu un développement vertigineux. En effet, peu de temps après les premiers vols, ‘industrie connaît une forte croissance avec l’importance de paviation lors des deux guerres mondiales.
On passe brutalement à une production en grande série, certains modèles d’avions étant même construits à plus d’un millier d’exemplaires. Aujourd’hui, l’industrie de raéronautique tient une place majeure dans l’économie mondiale. En effet, en 2012, le chiffre d’affaire du secteur s’élevait à plus 692 milliards de dollars. De plus, une nouvelle tendance se dessine : par rapport à 2011, le chiffre d’affaires de l’aéronautique civile a augmenté de et rattrape ainsi rapidement le secteur de la défense qui lui diminue de En France, en 2012, l’industrie aéronautique a généré 170 000 emplois (plus de 310 000 emplois avec les sous-traitants) pour un chiffre d’affaires de 42,5 milliards d’euros.
C’est une industrie fortement exportatrice (75% de son chiffre d’affaires est réalisé à l’export), qui a un poids déterminant dans la balance commerciale de la France. L’industrie aéronautique, spatiale, d’électronique, de défense et de sécurité française constitue ainsi le premier secteur exportateur ainsi que le premier en termes d’excédent commercial, avec plus de 20 milliards apportés à la balance commerciale française. En outre, ce secteur onsacre 906 millions d’euros à la recherche et au développement avec de nombreuses retombées pour les autres secteurs industriels. PAGF s OF sortant. C’est pourquoi le niveau d’un stock peut être évalué par une durée d’écoulement.
On dira par exemple que la quantité en stock permet d’assurer 10 jours de fabrication, jusqu’? épuisement du stock, sous l’hypothèse d’un flux entrant nul. La gestion des stocks est indissociable de la gestion des flux, et toutes deux dépendent de l’organisation physique de l’approvisionnement, de la production, de la logistique et de la commercialisation. Les différents types de stocks On distingue en général quatre types de stocks, dont le rôle et l’importance stratégique dépendent beaucoup de Pactivité de l’entreprise et des relations qu’elle entretient avec ses fournisseurs et clients : – les matières premières : pour de nombreuses entreprises, elles constituent le point de départ du cycle productif.
Souvent stockées avant d’être utilisées ou transformées, leur gestlon est essentielle au bon fonctionnement du processus de production et notamment à sa « fluidité » – les en-cours et les composants : ils peuvent être externes (achat à un fournisseur) ou internes (production stockée). Dans les deux cas, il est nécessaire d’en planifier parfaitement les besoins. Parce que les multiples opérations du processus de production sont rarement synchronisées de façon parfalte, elles vont produire des en- coursl qu’il sera nécessaire de stocker avant une prochaine utilisation. Les stocks d’en-cours ou de composants prennent le nom de « stocks de fabrication Ce sont les types de stock PAGF 6 OF s dans le secteur de comme un produit fini. les produits finis et les marchandises : les stocks associés sont alors appelés « stocks de distribution Les caractéristiques habituelles de la demande de es produits (les consommateurs sont nombreux, la demande est certaine ou probabilisable) autorisent la construction de modèles dans le but d’optimiser la gestion de stocks. – les fournitures : il s’agit des éléments consommés lors du cycle productif, mais qui ne sont pas des constituants du produit (l’énergie par exemple). Contrairement à ce qui précède, les méthodes visant à gérer les stocks de fournitures s’appuient sur des démarches empiriques et ne sont généralement pas considérées comme stratégiques. Il reste possible de faire des économies à ce niveau.
B) Les principaux systèmes de gestion des stocks L’efficacité des systèmes de gestion de stocks passe par la maîtrise temporelle et quantitative des approvisionnements, et notamment par une parfaite connaissance de la demande de l’entreprise, ainsi que des informations sur les fournisseurs. Nous allons maintenant évoquer les différents systèmes de gestion de stock. Dans le cadre de la gestion des stocks d’une entreprise : le flux amont est régulé (production) alors que le flux de sortie ne l’est pas car l’entreprise ne maîtrise pas la demande. Finalement, dans le court et mo en terme, le seul moyen d’agir sur le niveau du stock con PAGF 7 OF couple « quand ? -combien ? ?? dépendent de plusieurs éléments, sur lesquels l’entreprise n’a pas la même maîtrise : le secteur d’activité et des objectifs généraux de l’entreprise le niveau actuel du stock la nature du produit et sa demande – la demande future Il faudra donc répondre à la question « quand commander » ? l’aide du tableau suivant Le système à point de commande Une commande est déclenchée dès que le niveau du stock devient inférieur ou égal au stock d’alerte, encore appelé point de commande, ou selon la terminologie anglo-saxonne ROP pour reorder point En règle générale, le volume des commandes successives est fixe t déterminé à l’aide du modèle de la quantité économique Le système de gestion calendaire à niveau de recomplètement La gestion calendaire suppose l’examen du stock à intervalles de temps réguliers, par exemple, le 28 de chaque mois. À ces dates fixes, il faudra passer une commande d’un volume égal à ce ui a été consommé pendant la pér PAGF B OF alors évaluer au mieux la demande ainsi que l’offre émanant du marché afin de constituer les stocks de manière optimale pour pouvoir satisfaire au mieux les clients. La méthode MRP est une méthode de planification des besoins en composants basée ur la nomenclature des produits. Le M. R. P. ‘applique particulièrement bien aux entreprises fabriquant des produits à nomenclatures complexes avec variantes et options possédant des composants communs, avec une demande prévisible et une fabrication discontinue de lots. C’est le cas des entreprises du secteur aéronautique (et aussi électroniques, mécaniques, électromécaniques, textiles… ) Le MRP va connaitre de nombreuses évolutions au cours du temps. En effet, au début c’est-àdire dans les années 1960, la méthode utilisée est appelée Materials requirement Planning (Planification des besoins en composants). On l’appelle aussi MRP O. Dans cette méthode, suite aux prévisions de la demande et des délais précis, l’entreprise définit la quantité de composants dont elle doit s’approvisionner.
Le MRP ne représente donc à cette époque qu’une méthode de « calcul des besoins matières Cependant, elle s’avère incomplète puisque celle-ci n’intègre pas la gestion de toutes les ressources de l’entreprise à savoir les ressources en main d’œuvre et en capital nécessaires pour la fabrication du produit fini. Vient alors la deuxième méthode appelée Manufacturing resource Planning (Planification es ressources productives). On l’appelle aussi le MRP-I, il a été développé en 1970. Cette méthode vient évincer le ntionné dans la méthode production lors de la planification. Malgré cette solution, un autre problème se pose : cette méthode ne prend pas en compte le rôle des finances dans la chaine de production c’est-à-dire les coûts que génère l’entreprise. En effet, le MRP-I se focalise uniquement sur l’aspect productif.
Le MRPI va ensuite évoluer vers un système avec adéquation charge / capacité. Autrement dit, il devient une « Méthode de régulation de la production ». On aboutit alors à la troisième version du MRP, c’est le MRP-2. Développé en 1979, ce dernier rajoute au calcul des besoins, la recherche de l’adéquation entre charges et capacités. L’objectif étant ici de fabriquer ce que l’on peut, de respecter les délais et de réduire les coûts de production. La prise en compte de ces paramètres va permettre une certaine performance dans le moyen terme. Cette méthode étant la plus utilisée aujourd’hui, celle-ci sera donc plus détaillée à travers le fonctionnement du MRP.
Après cette évolution vers le Management des ressources de la production, dans les années 980, le MRP est associé aux techniques « juste à temps et de qualité c’est le MRP 2 ? délai court. Enfin dans les années 1990, la gestion de production est devenue un maillon central de l’entreprise, réellement intégré avec les autres fonctions. Le MRP évolue vers le ERP(planification des ressources de Pentreprise). Le MRP-I conçu par J. Orlicky a été rendu opérationnel quelques années plus tard par Orlicky lui-même et deux spécialistes de la gestion de production, Plossl et Wight. II semblerait que le MRP-2 ait été résenté par Wight Alliourd’hlli, seul le MRP-2 nt que méthode de