Granulation Sofiane
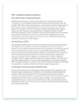
Introdution Dans le domaine de la formulation et de la mise en forme solide, l’élaboration d’un produit possédant toute les qualités requises nécessite de mettre en jeu le couplage de deux classes de paramètres : La première correspond aux paramètres thermodynamiques (ou physico-chimiques) locaux dépendant de la nature des liants et des poudres qui rentrent dans la composition du produit final. La deuxième correspond aux paramètres des procédés qui sont susceptible d’intervenir tout au long d’étapes de fabrication.
Tout au long de ce travail, les deux classes de paramètres seront revues àfin de GRANULATION. Objectif • rôler l’opération de org Sni* to View La granulation a pour but de transformer des particules de poudres cristallisées ou amorphes en agrégats solides plus ou moins résistants et plus ou moins poreux appelés granulés ou grains. Selon la destinée du grain, celui-ci doit présenter un certain nombre de propriétés. our la fabrication des comprimés il doit répondre par les propriétés galéniques suivantes : -DÉcoulement rapide g 10 s -OTassement wo – VSOO 20 ml Non friable & bonne aptitude à la compression Granulométrie homogène Humidité résiduelle très faible (2 à 6%), etc… easons for granulating a pharmaceutical compound are listed as follows: 1. To increase the uniformity of drug distribution in the product 2. To densify the material 3. To enhance the flow rates and rate uniformity 4. To facilitate metering or volumetric dispensing 5. To reduce dust 6.
To improve the appearance of the product B. Modes de liaison entre les particules : L’agglomération des particules dépend des propriétés physico- chimiques des prodults. La plupart des travaux réalisés dans le domaine de l’agglomération exploite les conclusions des études de Rumpf [1958, 1974]. Cet auteur a recensé les différentes liaisons existant ntre les particules solides, en présence ou non de lien matériel. Il a montré la contribution des forces interfaciales, des couches adsorbées, des liaisons capillaires et des forces intermoléculaires d’attraction.
Ces liaisons peuvent être divisées en deux groupes (Figure I-1): 1 . les liaisons existant en présence de lien matériel :CHANGER – les ponts solides, crées par transfert de matière (fusion, frittage, recristallisation de substances dissoutes, réaction chimique), – les ponts quasi- liquides, peu mobiles ou a mobilité restreinte, engendres par des macromolécules ou des polymères de haute iscosité qui forment des liaisons fortes très proches des ponts solides, – les liaisons dues a des liquides mobiles (ponts liquides) et crées par des forces de capillarite et de tensions interfaciales. . les liaisons existant sans lien matériel : *AGF 9 rif q particules, – les liaisons de type Van der Waals, hydrogènes, électrostatiques, magnétiques. Ces liaisons immatérielles ne peuvent s’établir que si les distances interparticulalres sont fables. Les forces d’attraction deviennent efficaces quand les particules sont distantes de moins de 0,01 Zm- Elles sont négligeables pour des istances supérieures a 1 Zm. D’autre part, elles jouent un rôle prépondérant quand la taille des particules est inferieure a 100 Zm.
Compte tenue de l’irrégularité de surface de la plupart des solides, il ne pourrait pratiquement jamais s’établir de telles liaisons. Cependant si le matériau est suffisamment plastique, les déformations pendant l’agglomération peuvent niveler les Irrégularités de surface et créer les surfaces de contact necessalres. Figure 1-1 Force de liaisons La Figure 1-2 représente l’importance des différentes liaisons interparticulaires en fonction de la taille des particules.
Les liaisons immatérielles sont les plus faibles, elles lient préférentiellement les petites particules. Les liaisons les plus fortes sont dues aux ponts solides. Les travaux de Schubert [1981] permettent de mieux comprendre l’importance des différentes forces élémentaires intervenant lors de la cohésion en fonction de la taille des particules. Il a montré que pour les particules de tailles inferieures a 100 Zm, les forces de Van der Waals sont prédominantes par rapport aux autres forces intervenant lors de la cohésion sans lien matériel.
Outre la taille des particules, la rugosité de la surface des particules a également ne influence non négligeable sur les forces d’adhésion [Rumpf, 1974]. En les t également une influence non négligeable sur les forces d’adhésion [Rumpf, 1974]. En effet, les travaux de Schubert ont montre que, pour des valeurs inferieures a 10-2Zm, les aspérités présentes a la surface du solide augmentent la distance entre les particules et diminuent donc les forces d’adhésion interparticulaires.
Au delà de cette valeur, on observe les phénomènes opposés. En ce qui concerne les ponts liquides, leur intensité dépend du volume de liquide présent dans le ménisque et ce par ‘intermédiaire de l’angle de mouillage solide/liquide. Schubert [1981] a démontré que pour des valeurs de l’angle de mouillage supérieur a 700, la force d’adhésion ne varie pratiquement pas avec la distance entre particules.
Figure 1-2 La résistance a la traction selon les différents mécanismes de liaison en fonction de la taille des particules S DE GRANULATION; LES 2 GRANULATIONS HUMIDE ET SÈCHE: Theorie La granulation est un exemple de design de particules, les attributs désirés des granules sont controllés par une combinaisaon de la Formulation et du Procédé, Les méthodes de granulation peuvent être divisées en deux éthodes majeures : Granulation Humide qui falt appel aux liquides pour lier les particules, et la Granulation Sèche qui ne fait appel à aucun liquide.
Fieure 1 Various granulatio mm et une porosité élevée (entre 20 et 50%), sont appelés granules. Si ces agglomérats Sont sphériques et ont une distribution de taille resserrée comprise entre et 2 mm et une faible porosité (environ 10%), le processus est référé a la pelletisation et les agglomérats formes sont appelées pellets. En général, le mouvement des particules entre elles, conditionne les propriétés du produit (Taille, distribution de taille, compacité, porosité).
Suivant la nature du produit désiré, pellets ou granules, il existe différentes technologies qui se différencient par le moyen employé pour assurer la mise en mouvement des particules solides au sein de l’appareil. Ainsi on peut distinguer : – l’agglomération par agitation mécanique : les appareils les plus utilises sont les graduateurs a cuve fixe équipe d’organes internes mobiles. Le mélange de la poudre et de la phase liquide, ainsi que la croissance des agglomérats a lieu par agitation mécanique.
En général, la pelletisation est fréquemment réalisée dans ce type d’appareil, l’agglomération par roulement : les appareils les plus utilises sont les assiettes tournantes et les tambours rotatifs. Sous l’effet de rotation, les particules roulent les unes sur les autres et s’agglomèrent entre elles. La distribution du liquide dans le lit de poudre est déterminante en granulation humide. Elle impose le mode de croissance ainsi que les propriétés des granules.
Ainsi, le mélange entre la poudre et le liquide est une opération clef pour la granulation humide. Le processus de mélange est directeme anismes qui qui conditionnent la mise en mouvement des particules au sein de l’appareil. Selon certains auteurs [Lacey, 1954] et [Singh, 1987], on peut distinguer trois mécanismes de mélange – Mélange par diffusion : il s’agit d’un déplacement individuel des particules initie par des chocs et aboutissent a une distribution individuelle des particules.
Les appareils dans lesquels ce mécanisme est dominant, sont les appareils a cuve rotative, a chocs et a percussion – Mélange par convection : dans ce cas un ensemble de particules est mis en mouvement par un mobile au sein du mélangeur. Ce mécanisme est prédominant dans les mélangeurs a ruban, a vis sans fin. Mélange par cisaillement : dans ce cas, apparait un ensemble de lan de glissement de couches de particules dans le mélange sous une action mécanique. Le mouvement relatif de ces plans implique un brassage des particules.
En général, la granulation peut être réalisée a faible taux de cisaillement, par exemple en lit fluidise, ou le mouvement des particules est induit par le courant d’air, et a taux de cisaillement élevé ou intermédiaire, ou le mouvement des particules est assure mécaniquement par des agitateurs ou par le mouvement de la cuve. La granulation a taux de cisaillement intermédiaire est souvent réalisée en tambour rotatif ou en assiettes tournantes andis que la granulation a taux de cisaillement élevé s’effectue dans des mélangeurs granulateurs équipés par des pales a mouvement rapide.
La figure 1-3 présente quelques des granulateurs utilises p tion en voie humide et la pelletisation. Figure 1-3 Presentation schematiques de dispositifs d’agglomeration : a. tambour rotatif ; b et c. melangeur granulateur ; d. equipement d’extrusion/ spheronisation Contrôle du grain qd g humide : 60 CllJEssai d’écoulement* (Ph. Eur- 2. 9. 16. ) L’essai d’écoulement est destiné à déterminer l’aptitude des poudres et des granulés à s’écouler verticalement. La mesure de la fluidité se fait à l’aide d’entonnoir de dimensions standardisees ou normalisées.
La facilité d’écoulement d’un mélange de poudres ou d’un grain est importante pour sa répartition volumétrique surtout lorsque celle-ci doit être rapide [exemple, cas de la compression]. La fluidité est fonction d’un grand nombre de facteurs granulométrie, forme, humidité résiduelle, densité, électricité statique, etc * Test réalisé en Travaux homogènes, mais dans celui des grains destinés à la fabrication des comprimés, une certaine proportion de « fines » peut être ouhaitable pour un meilleur remplissage de la matrice.
CIOMesure de l’humidité résiduelle L’humidité résiduelle d’un grain influence un certain nombre de ses propriétés [la conservation du principe actif par exemple]. La mesure de l’humidité résiduelle d’un grain peut être déterminée à l’aide de dessiccateur à infrarouge [dessiccateur : MettierLJ 16]. Il est nécessaire de mesurer l’humidité résiduelle du grain. Elle est en général comprise entre 2 à 6 Dans le cas de la fabrication des comprimés ; DÛGrain trop sec : la cohésion sera insuffisante et les comprimés auront tendance à se cliver (décalottage).
DÜGrain trop humide : l’écoulement se fera mal et le comprimé collera à la matrice (grippage) et aux poinçons (collage). Effet des paramètres thermodynamiques et opératoires sur la granulation humide à fort taux de cisaillement!!!!!!!!!! Les nouvelles technologies : le monde pharmaceuqtie est toujours à la recherche de formes galéniques innovantes, ou d’un portefeuille de technologies indispensables à la conception de médicaments innovants, permettant ainsi le renforcement de la protection des gammes de produits et/ou le développement de médicaments génériques.
Les technologies brevetées de Galenix sont les suivantes : MINEXTAB@ : technologie faible taux d’excipients qui permet de développer des comprimés avec un pourcentage d’au moins go % de principe actif. Cela permet de gérer des profils de libération immédiate, modifiée ou prolongée. MINEXTAB@ floating : technologie flottante qui permet au comprimé d – MINEXTAB@ floating : technologie flottante qui permet au comprimé d’être localisé en partie haute du tractus gastro- intestlnal.
Cette technologie utilise aussi les principes de libération de MINEXTAB@. MIJCOLYS@ : technologie dédiée à l’application mucosale et buccale. MUCOLYS@ Flash permet de libérer des molécules actives en ublingual et lingual sous forme de poudre à délitement inférieur? 5 secondes. – MUCOLYS@ Film permet de libérer des molécules à travers la muqueuse buccale par formation d’un film à partir d’une poudre. Technologie destinée à réduire et supprimer l’effet du 1er passage hépatique.
MICROGIX@ : technologie dédiée à l’amélioration de biodisponibilité et/ou solubilité de principe actif sous forme de poudre directement intégrable dans de multiples formes pharmaceutiques et sous différents mécanismes de libération. There are, however, a number of products that require low dose of drug ubstance, where the blend uniformity and the content uniformity in the drug product are critical. Traditionally, the assessment of the blend uniformity is done after the blending process is complete.
This required considerable delays in obtaining results, and the sampling techniques and product discharge from the blender required consistency to obtain satisfactory results. However, With the current interest in process analytical technology (PAT) on-line measurement of ingredients is possible. The U. S. Food and Drug Administration (FDA) has recently released guidance for industry detailing the current thinking on PAT (7). *AGF g c,Fq