Compte Rendu Moldflow
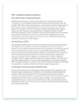
Table des matières Introduction 2 Phase de simulation 2 1) Identification du temps de maintien optimal 2 2) Identification de la pression maintien optimale 3 3) Identification de la vitesse d’injection optimale 4 4) Identification de la température optimale. 6 5) Conclusion 7 or 5 Sni* to View Introduction Avant tout, ce TP a pour but de d couvrir le logiciel Autodesk Simulation Maldflow Insight et de l’appliquer à nos éprouvettes vues lors du TP d’injection.
L’objectif visé est d’identifier l’influence des différents paramètres sur la masse finale de l’éprouvette, t ainsi d’en déduire par simulation les paramètres optimaux d’injection. Ces différents paramètres sont : le temps de maintien optimal la vitesse d’injection optimale la pression de maintien optimale la température optimale Phase de simulation 1) Identification du temps de maintien optimal simulations ont été regroupées dans le tableau ci-dessous.
Figure 1: Synthèse des résultats obtenus en faisant varier le temps d’injection A partir de ces valeurs, nous pouvons représenter graphiquement l’évolution de la masse de la pièce en fin de phase d’injection et en fin de phase de maintien, et ce en fonction du temps de aintien réglé antérieurement. Figure 2: Evolution de la masse de la pièce en fonction du temps de maintien à deux étapes différentes du processus La détermination du temps de maintien optimal se fait par la méthode des asymptotes.
Leur traçage permet par intersection et projection de l’identifier. C’est ainsi que dans notre cas nous avons trouvé un temps de maintien optimal d’environ 1 1,3 secondes. Remarque On remarque que plus le temps de maintien est grand, plus la masse de l’éprouvette augmente car avec le temps, la matière refroidit, se rétracte et libère donc du volume. A ce moment, la ouvelle matière comble cette place. Il y a donc plus de matière et donc plus de masse au final. ) Identification de la pression maintien optimale Cette deuxième phase de simulatlon s’effectue en utilisant le temps de maintien optimal précédemment trouvé. Elle a pour but d’identifier la pression de maintien optimale. Les calculs effectués sur Moldflow se font en faisant varier le pourcentage de pression de remplissage de à 120%_ Les uatre paramètres relevés *AGF 9 rif s varier le pourcentage de pression de remplissage de à 120%. Les quatre paramètres relevés sont les mêmes que dans la remière phase.
L’ensemble des valeurs calculées est reporté dans le tableau ci-après. Figure 3: Synthèse des résultats obtenus en faisant varier le pourcentage de la pression de maintien Il nous a ainsi été possible de tracer l’évolution de la masse en fonction en fonction du pourcentage de pression de remplissage. Figure 4: Evolution de la masse de la pièce en fonction du Encore une fois, la méthode d’identification de la pression de maintien optimale se fait par intersection des asymptotes.
Cela nous a permis d’identifier une pression de maintien de 24 % de pression de remplissage (MPa). Remarque : On remarque que la masse augmente avec la pression d’injection de la matière, de telle sorte à atteindre une valeur limite. Nous avons essayé par différentes tentatives expérimentales d’obtenir le meilleur compromis entre la masse de l’éprouvette et la pression (niveau énergétique) à fournir. 3) Identification de la vitesse d’injection optimale La troisième phase est la détermination de la vitesse du piston optimale. our l’obtenir, nous avons fait varier la vitesse du piston (en % de vitesse) dans le but d’obtenir les différentes masses avec le temps optimal et la pression optimale trouvé uparavant. Nous avons inscrit c auparavant. Nous avons inscrit ces différentes valeurs dans le tableau ci-dessous : Figure 5: Synthèse des résultats obtenus en faisant varier le pourcentage de la vitesse du piston Figure 6: Evolution de la masse de la pièce en fonction du Nous utilisons pour la troisième fois la méthode d’identification par intersection des asymptotes dans le but de trouver la vitesse de piston optimale.
En trouve que cette vitesse est de de la vitesse du piston. On remarque que plus la vitesse du piston est faible, plus la masse de l’éprouvette est importante. Nous pouvons expliquer e phénomène par le fait la matière libère de la place en se rétractant pendant son refroidissement. 4) Identification de la température optimale. Dans cette derniere partie du TP, nous avons dû faire varier la température de la matière afin d’observer l’évolution de la masse de l’éprouvette avec le temps optimal, la pression optimale et la vitesse de piston optimale précédemment trouvée.
Nous avons inscrit ces différentes valeurs dans le tableau ci-dessous . Figure 7: Synthèse des résultats obtenus en faisant varier la température d’injection D’après nos recherches (site internet et logiciel), nous avons rouvé que la température de fusion est de 2300C. Nous prenons donc en compte uniquement les valeurs après cette valeur, car avant cette dernière, le matériau est caoutchouteux.
On remarque que la masse diminue plus la température est élevée. Nous obtenons donc que la température optimale d’injection est de 2300C. 5) Conclusion Pour résumé notre TP, avec l’aide du logiciel MoldFlow, on a pu obtenir les différents paramètres d’injection qui permet d’avoir le meilleur compromis entre dépense énergétiques et qualité de notre pièce injectée (éprouvette). Nous obtenons : -Temps de maintien optimal 1 1. econdes -Pression de maintien optimale = 24 % de pression de remplissage (M Pa) – Vitesse d’injection optimale = vitesse de piston -Température optimale = 230DC Pour conclure, ce TP nous a permis de se familiariser avec le logiciel MoldFlow, ainsi que de connaître les différents paramètres d’injection, tout comme le moyen d’optimiser l’injection de matière. Nous aurions aimé comparer ces résultat avec les chiffres obtenus lors de la pratique sur la machine d’injection, mais malheureusement par la faute de la journée internationale sur la Chine, nous n’avons pas eu l’occasion de le terminer.