Marketing
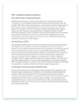
Les agents d’assemblage devaient être capables d’attraper les yeux fermés les bonnes pièces et les bons outils au vu du prochain odèle. Des râteliers mieux adaptés, des conteneurs et des installations de rangement furent conçus pour l’alimentation des pièces et le rangement des outils dans la bonne position. Les travaux préparatoires (qu’aujourd’hui on désignerait comme pré automatisation ) furent réussis. Le premier janvier 1983 la ligne principale d’assemblage était complètement transformée pour fonctionner en production segmentée.
A cette époque le volume de production était d’environ 200 motos par jour. Ces 200 se répartissaient comme suit : 100 KZ440S, 60 KZ650S et 40 KZIOOOS. Question 1. our cette combinaison donner une suite idéale pour une production segmentée Question 2. L’assemblage segmenté peut-il présenter quelque intérêt en période de récession des ventes de motos et d’accroissement des stocks de motos (comme ce fut le cas en 1982) ? Production segmentée dans la fabrication des pièces de moto Le principal sous ensemble fabriqué à l’usine de Lincoln est sans doute le cadre de moto.
Les pièces du cadre sont fabriquées partir d’un stock de tubes d’acier et leur soudure donne le cadre. A l’époque, les pièces du cadre étaient lancées en fabrication sur es presses à étamper par lots de plusieurs milliers d’unités. Ces lots importants étaient économiques parce qu’il fallait normalement une demie journée ou 20 Ces lots importants étaient économiques parce qu’il fallait normalement une demie journée ou plus pour amener un moule pesant à sa place sur une grosse presse et effectuer tous les réglages et contrôles de la machine correctement.
Les essais constituaient une composante du temps de changement : inspection de la dimension des pièces, modification des réglages, essais et inspection d’autres pièces et ainsi de suite. Question 3. Expliquer la logique de lot à laquelle obéissait Kawasaki ? En 1980-81 les presses furent modifiées pour permettre des changements d’outils et des réglages rapides. Des sections de convoyeurs ordinaires à rouleaux furent soudées pour former un « carrousel » tout autour de la presse ; toutes les matrices furent mises à niveau de telle sorte qu’elles avaient des « hauteurs fixes » standards.
L’insertion et la fixation furent simplifiées. Une douzaine ou plus de matrices pouvaient être alignées autour du convoyeur à carrousel le matin. Chaque matrice pouvait apidement et avec précision être mise en place durant la journée par l’échange d’une pièce d’un cadre avec une autre. La modification fit passer le temps de lancement en dessous des dix minutes (incluant une durée de contrôle nulle). Au lieu de faire des milliers d’unités d’un modèle, il devint économique de travailler par lot de 200, 100, voire 50.
Bien que ce ne fût pas encore la taille idéale de lot 1, on s’en rapprochait. Question 4. Comment caractériseriez-vous le changement de série opéré par Kawasaki ? A quelle méthode fait-il référence et quels en sont les points forts ? Mais Kawasaki voulait accomplir l’idéal : le changement de fabric Mais Kawasaki voulait accomplir l’idéal : le changement de fabrication en une seule touche et la production des pièces à l’unité. Ce but fut atteint pour les pièces de cadre à forte utilisation au cours de l’été 1982. our parvenir au changement en une seule touche, on remplaça les grosses presses polyvalentes à étamper par de petites presses à vis à usage spécialisé. Chaque presse à vis possédait une matrice intégrée de telle sorte qu’il n’y avait plus de changement d’outil et donc zéro temps de changement de série – une machine dédiée. La pression pour les presses à vis s’exerçait progressivement au lieu d’un coup unique ; mais ce qu’on perdait en vitesse était largement compensé par l’absence de changement de série.
De plus les matrices étant correctement positionnées une fois pour toute, le risque des pièces défectueuses était moindre. Actuellement les presses à vis sont situées dans l’atelier de soudure où un soudeur peut préparer plusieurs presses pour fabriquer des pièces de cadre différentes. Au fur et à mesure de l’achèvement de chacune l’ouvrier peut la souder immédiatement sur le cadre en cours e réalisation. Il ny a pas de stock lié à la logique de lot.
On a supprimé la plupart des presses à étamper puisque maintenant les ouvriers réalisent les pièces en fonction de l’état d’avancement des cadres. Question 5. Quelles économies ont été réalisées par Kawasaki avec le carrousel? Quels sont les intérêts supplémentaires du changement en une seule touche par rapport à la solution du carrousel ? Annexe : la production segmentée En général les entreprises réalisent plusieurs mo 4 20 En général les entreprises réalisent plusieurs modèles différents de chaque produit fini.
La plupart des producteurs réalisent un lot important du premier modèle et ensuite d’un autre sur les mêmes machines ou ligne de production. Les fabricants en juste- à-temps ont développé des méthodes pour produire les modèles de façon segmentée, eest à dire en assortiment de simples unités de chaque modèle, l’un après Pautre, sur une machine ou une ligne de production. Les gains sont impressionnants. L’usine peut établir des programmes pour produire chaque jour à peu près le même assortiment de modèles que celui qui sera vendu ce jour.
On fabrique les bons modèles et le besoin de stocker de grandes uantités de produits finis va en diminuant. Il en va de même pour les sous ensembles et les composants : les bonnes pièces sont produites dans la même combinaison que celle qui sera utilisée. Ainsi les stocks sont faibles. De plus on peut économiser sur les capacités de pointe puisque de petites quantités de chaque modèle sont faites régulièrement. On peut utiliser des outils et des équipements plus simples dont la charge sera plus reguliere. our rendre économique la fabrication segmentée des pièces de composants, les machines et les lignes de production doivent être onstruites de telle sorte que les opérations liées à l’outillage, les réglages de machine, les codes pièce et les opérations de chargement-déchargement puissent être effectués rapidement. On parle de « changement rapide de fabrication un nombre de minutes à un seul chiffre – quand une machine peut être réglée en moins de dix minutes pour s 0 nombre de minutes à un seul chiffre – quand une machine peut être réglée en moins de dix minutes pour fabriquer un nouveau modèle.
Quand la machine ne requiert aucun réglage – juste les temps de chargement-déchargement – on parle de changement e fabrication en une seule touche. Figure A Produits Janvier Figure B Produits Jour 1 Février Jour 2 Mars Jour 3 6 0 d’un cycle de production répétitif. Pour rencontrer la demande quotidienne ce cycle sera répété 3 fois par jour. On cherche alors à l’intérieur du cycle de 13 unités la séquence qui minimise d’une part, l’intervalle de temps entre deux productions non consécutives du même modèle et d’autre part, le nombre d’unités d’un même modèle produites consécutivement.
Cette dernière étape peut nécessiter des tâtonnements, mais une ou deux tentatives suffisent en général. Par exemple : 1. LLI_LLLLLMMMMN répété trois fois par jour implique 5 unités entre deux séries distinctes de 8L, 9 unités entre deux séries distinctes de 4M et 12 unités entre deux séries distinctes de IN 2. LLMLLMLLMLLMN répété trois fois par jour implique 2 unités au maximum entre deux séries distinctes de 21_, 3 unités au maximum entre deux séries distinctes de IM et 12 unités entre deux séries distinctes de IN Traduit de R.
Schonberger, World Class Manufacturing Casebook, The Free Press, 1987 et de R. Schonberger et E. Knod, Operations Management, Irwin, 1991 eUniversité de CAEN UE7 – GESTION DE LA PRODUCTION Date : samedi 10 juin 2006 2ème semestre Durée: 2 heures -9h OO- 11 hoo Lincoln dans le Nebraska. Un des objectifs des nouveaux dirigeants était de transformer la ligne principale d’assemblage en production segmentée. La ligne produisait des lots d’au moins 200 unités de chaque modèle entre deux changements de série. eux actions préliminaires précises • ainsi de suite devaient être clairement étiquetés de telle sorte qu’un agent d’assemblage devait être capable instantanément d’identifier et de sélectionner le bon article. Lorsque les modèles hangent de l’un à l’autre sur le convoyeur, des retards dans l’identification des bonnes pièces et des bons outils peuvent être intolérables. Un système de codes couleur fut imaginé pour que, par exemple, tous les articles se référant à la moto KZ650 fussent étiquetés avec une pastille gommée rouge.
Même la position de la pastille sur le carton, la pièce ou l’outil devait être précisément indiquée. 2. L’emplacement. Les ingénieurs, les inspecteurs matière, les contremaîtres, et agents d’assemblage dressèrent l’emplacement exact des pièces et outils aux postes de travail le long de la ligne ‘assemblage. Les agents d’assemblage devaient être capables d’attraper les yeux fermés les bonnes pièces et les bons outils au vu du prochain modèle.
Des râteliers mieux adaptés, des conteneurs et des installations de rangement furent conçus pour l’alimentation des pièces et le rangement des outils dans la bonne position. pré automatisation ) furent réussis. Le premier préparatoires (qu’aujourd’hui on désignerait comme pré automatisation ) furent réussis. Le premier janvier 1983 la ligne principale d’assemblage était complètement transformée pour fonctionner en production segmentée. KZ440s, 60 KZ650s et 40 KZIOOOs. Question 1.
Pour cette combinaison donner une suite Idéale changements d’outils et d pi furent modifiées pour permettre des changements d’outils et des réglages rapides. Des sections de convoyeurs ordinaires rouleaux furent soudées pour former un « carrousel » tout autour de la presse ; toutes les matrices furent mises à niveau de telle sorte qu’elles avalent des « hauteurs fixes » standards. L’insertion et la fixation furent simplifiées. une douzaine ou plus de matrices pouvaient être alignées autour du convoyeur à carrousel le matin.