Le Lean Management
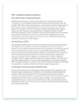
Introduction Au cours de ces deux dernières années, les grandes entreprises du monde entier ont dû faire preuve de souplesse et d’adaptation pour pouvoir surmonter efficacement la récession économique et, plus récemment, pour être en mesure de tirer profit de la reprise économique apparente. Parallèlement à cette dynamique de marché, partout dans le monde, des sociétés ont adopté le Lean Management, un catalyseur clé de leur survie et de leur rebond. Le Lean management est ensemble de techniques visant ? l’élimination de toutes les activités à non valeur ajoutée. ? Lean » n français signifie « fait une technique de s org réduction des pertes né. une production et un gement est de ce t. concentrée vers la ne organisation, pour attendue de le faire dans les meilleures conditions. Le Lean management (littéralement « gestion maigre », « sans gras ») est une méthode d’ organisation du travail en entreprise, originaire du Japon . Le ean est une philosophie de gestion provenant principalement du Toyota Production System (TPS) de l’entreprise Toyota (d’où le terme toyotisme, également répandu). Le concept s’appliquait à l’origine au Manufacturing (KANBAN,
SMED, TPM, Zéro-défaut). Les Américains Vont étendu ? l’ensemble de l’entreprise en lui donnant un cadre théorique cohérent. Le Lean management est un système d’ organisation du travail qui cherche à mettre la contribution l’ensemble des acteurs afin d’éliminer, selon les adeptes de ce système, les gaspillages qui réduisent l’efficacité et la performance d’une entreprise, dune unité de production ou d’un département notamment. Pour cela, le Lean se fixe comme objectif d’éradiquer trois « démons » de l’organisation du travail : Muda Sans valeur : tout ce qui est sans valeur
Les gaspillages, ce qui est fait mais qui n’ajoute pas de valeur au produit — c’est- à-dire ce qui finit à la poubelle —, les pannes, les déplacements inutiles, les pertes de temps, les choses que l’on ajoute au produit, mais dont le client ne veut pas, etc. Muri : l’excès, la surcharge de travail engendrée par des processus non adaptés : Le personnel, lorsque la charge de travail n’est pas adaptée au nombre de travailleurs ; Les installations, lorsque la charge est supérieure à ce qu’une installation peut faire (sa capacité) ; Les stocks, lorsque des pièces ou des produits ne « tourne
Les stocks, lorsque des pièces ou des produits ne « tournent pas Mura : la variabilité, ou l’irrégularité Des machines qui ne mettent pas toujours le même temps pour faire la même chose et dont la qualité varie ; Des opérateurs qui ne font pas tous et pas toujours le même travail lorsqu’ils sont affectés à un même poste ; Des fournisseurs qui ne livrent pas toujours les mêmes quantités de matière première.
Le Lean management s’attaque particulièrement à sept formes de gaspillage la surproduction, les attentes, les rebuts- retouches/corrections, les gammes et processus opératoires mal adaptés, les transports/ uptures de flux, les mouvements inutiles et les stocks (productifs ou administratifs) ; auxquels il faut ajouter un huitième gaspillage, qui est la non-utilisation des ressources intellectuelles du personnel.
DÉROULEMENT ET MODALITÉS D’ORGANISATION 1 . Un diagnostic est d’abord réalisé, sous forme de MIFA (Material Information Flow Analysis. Cette méthode vise à analyser les flux de matière et les flux d’information sur l’ensemble du processus de production, depuis la commande du client jusqu’à la livraison du produit ou seNice. Lors de ce diagnostic, les difficultés et les ources de gaspillage sont identifiées, pour chaque étape du processus.
Pour ce faire, un groupe de travail multi-disciplinaire doit être constitué (et animé par un consultant extérieur ou par une personne formée en interne). Il rassemble les différentes fonctions de l’entreprise (production, qualité, achats, logistique, méthodes, etc. ), afin d’obtenir un diagnost l’entreprise (production, qualité, achats, logistique, méthodes, etc. ), afin d’obtenir un diagnostic pertinent et complet.
En effet, les difficultés d’un processus de production se situent souvent à l’articulation des différentes fonctions de rentreprise. Le fait d’impliquer tous les services de l’entreprise permet également dobtenir un consensus sur la situation de départ, ce qui est crucial pour le choix des actions à mettre en oeuvre, et leur réalisation concrète (qui implique souvent elle-même plusieurs sen,’ices). 2. Sur cette base, des chantiers ou ateliers de travail sont identifiés et priorisés pour réduire les gaspillages.
Cela peut passer par une réduction des coûts, une amélioration de la qualité ou une réduction des délals. Différents outils tels que les 5S, ou le SMED, peuvent être utilisés pour ces chantiers (voir ection « Outils disponibles » ci-dessous). La prise en compte des coûts complets des déchets est intrinsèque à la méthode, car il s’agit de travailler sur toutes les étapes de la production. Les coûts de production et les coûts de gestion interne des déchets sont donc nécessairement intégrés au diagnostic initial.
Par exemple, si l’optimisation passe par une réduction des pertes matière lors d’une des étapes de la production, les quantités de déchets s’en trouveront réduites, ainsi que les coûts associés. 3. Pour un travail spécifique sur la production et la gestion es déchets, et en complément d’une démarche interne de Lean Manufacturing, il est possible de mener un travail de « développement fournisseur Ceci peut permettre une prise en compte directe PAGF mener un travail de « développement fournisseur Ceci peut permettre une prise en compte directe du coût de gestion externe des déchets.
Il s’agit pour un donneur d’ordre de proposer à son prestataire ou à son fournisseur (un prestataire d’enlèvement et de traitement des déchets par exemple) de mettre en place une démarche de Lean Manufacturing, afin d’optimiser l’ensemble de la chaîne. Il convient cependant de oter que cette démarche n’est pas toujours acceptée par le fournisseur ou le prestataire, qui peut nourrir des craintes liées ? la confidentialité de ses propres processus et des coûts associés. Dans ce cas, ce « développement fournisseur » peut être effectué par un consultant externe à l’entreprise donneuse d’ordre. . es opérations demandent une certaine maîtrise des outils proposés. Il est possible de faire uniquement appel à une expertise externe (cabinet de conseil) pour mener la démarche. Cependant, le Lean Manufacturing se présentant comme un processus d’amélioration continue, il peut être intéressant ‘intégrer l’expertise et la « culture Lean » au sein même de l’entreprise. pour ce faire, de nombreux cabinets proposent des « formatlons- actions » pour le personnel de l’entreprise.
Les salariés formés au Lean Manufacturing deviennent alors consultants internes spécialisés dans cette démarche. Ils peuvent également rester ? leur poste initial et y appliquer les principes et méthodes du Lean Manufacturing dans leurs opérations quotidiennes. Ces formations peuvent débuter par une formation en salle, puis un diagnostic conjoint, suivi d’un accompagnement des person ne formation en salle, puis un diagnostic conjoint, suivi d’un accompagnement des personnes porteuses d’un chantier sur six mois.
Le cabinet responsable de la formation suit alors chaque porteur de projet sur un chantier, le temps qu’il se mette en oeuvre. Ceci permet d’obtenir des résultats rapidement, et de en interne des compétences en Lean MOYENS À MOBILISER ET DÉLAIS DE MISE EN OEUVRE Ressources humaines : Plusieurs personnes ayant des postes différents sont impliquées dans le diagnostic initial afin de couvrir l’ensemble du processus. Dans l’idéal, ce groupe de travail initial est maintenu et animé our la mise en oeuvre de la démarche. Ressources techniques .
La maîtrise des outils du Lean Manufacturing nécessite un accompagnement et/ou une formation spécifique. Ressources financières L’accompagnement par un cabinet conseil est nécessaire lorsque les compétences ne sont pas présentes en interne dans l’entreprise. Le coût de cet accompagnement peut être très variable. Le choix de former des membres de l’entreprise aux méthodes et outils Lean Manufacturing représente également un coût, dont le retour sur investissement sera assuré en associant à la formation la réalisation de projets concrets
Approche méthodologique du Lean management Les outils du Lean Management Le Lean management, au delà d’être un ensemble de méthodes, repose sur le facteur humain. Il suggère que le personnel travaille dans un état d’esprit orienté vers la diminution du gaspillage et des pertes (de temps, de matières d’argent … j. La motivation et les comportements des ho pertes (de temps, de matières, d’argent La motivation et les comportements des hommes sont nécessaires pour une application efficace.
Ci-après, nous détaillons quelques outils du Lean management : Kaizen : Méthode encourageant à chaque niveau les petites méliorations quotidiennes, sans gros investissement et basées surtout sur le bon sens, contrairement à l’approche occidentale qui fonctionne davantage par grandes avancées souvent coûteuses et peu concertées. VSM (Value Stream Mapping) :Représentation graphique et documentée de la chaine de la valeur permettant d’en faire le diagnostic et de la repenser avec l’obsession d’éliminer les gaspillages.
SS :règles de base du comportement de l’opérateur vis-à-vis de sa machine (trier, ranger, nettoyer, standardiser, suivre) visant ? éliminer les pertes d’efficacité et à redonner de nouvelles sources de motivation, TPM (total productive maintenance): Méthode basée sur 8 piliers et fondée sur le respect des facultés humaines et la volonté participative de Fensemble du personnel pour rentabiliser au maximum les installations.
Taktime: Cest le D’thme correspondant à la capacité d’absorption du marché et sur lequel l’ensemble de l’entreprise doit se synchroniser afin de produire ni trop ni trop peu. Line Balancing: Directement issu de la Théorie des Contraintes (TOC), le LB consiste à orchestrer les flux autour des goulets afin de maximiser le débit global du système. SMED (single minute exch éthode systématique